William Garden's book
The Making of Tom Cat. tells the story of how he came to design this boat and provides more than a good preview of the plans, it's also a guide to the construction. The book explains the similarities the design has with the Beetle Cat design. Although not mentioned in the book, except for the hull length the design is more like the Beetle 14 with seats in the cockpit and the higher freeboard.
Photos of Bill Garden sailing Tom Cat from his book:
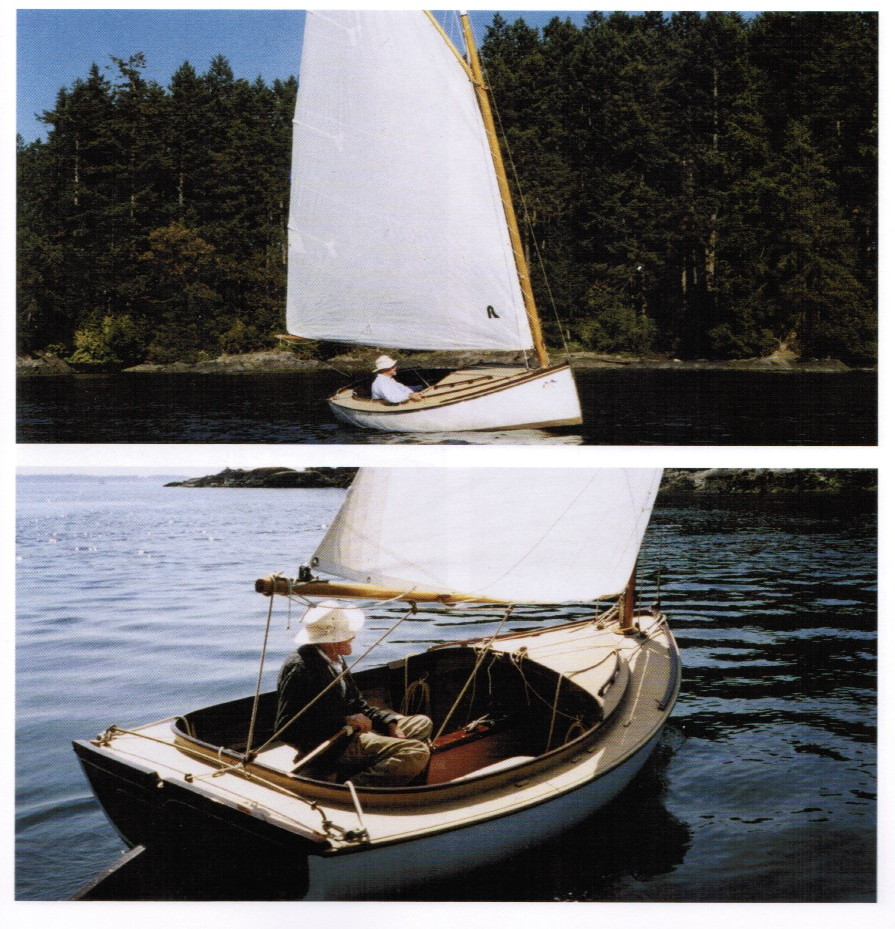
This is the Wooden Boat Store's link to photos of a
cold moulded version of Tom Cat's hull being built. The hull is shown laid up over ribbands with no ribs. (All in 5 days if I'm reading it right.)
There is an extensive WoodenBoat
forum thread with dozens of construction photos showing a beautiful strip built version of the hull. This builder chose to add ribs after hull construction. He provides a link to an Australian forum which walks through the steps in building the design.
This is a link to the
Beetle Cat 14 page. Scrolling down to the building photos, They install ribs
inside the ribbands. In both these Beetle hulls, planking is attached to the ribs as the hull is formed.
Oct 18 - 19th - Tested bending two 3/8" thick ribs together. That was better than trying the full 3/4" thickness but it didn't really work either. I did discover that I could straighten out a rib using my heat gun to fit back in the 4" wide steam box. That worked fine by doing each piece separately. Lofted out the stem and made a mold board for it.
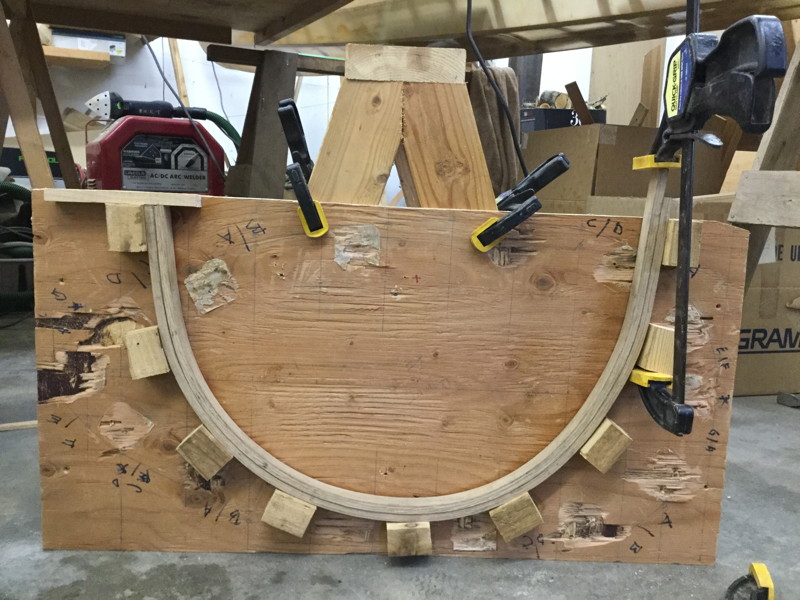
Oct 20th - Based on the results of my simulated rib bending and my experience with bending the ribs for my kayak plus the size of the ribs, I decided to make the molds for the ribs to fit inside the ribbands as is done with the Beetle 14 construction.
So... NO RIBS!!!. But the oven worked great for the stem laminations.
Nov 23-25th Milled up the remaining wheel parts, cut the 32 internal pieces...
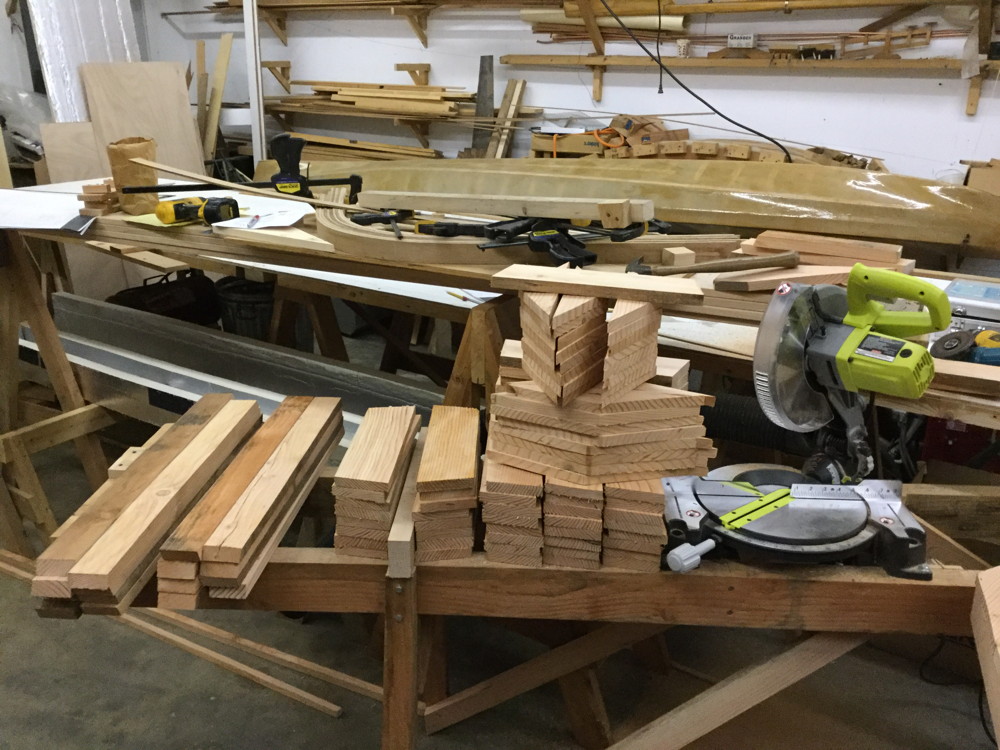
...fastened the first corner.
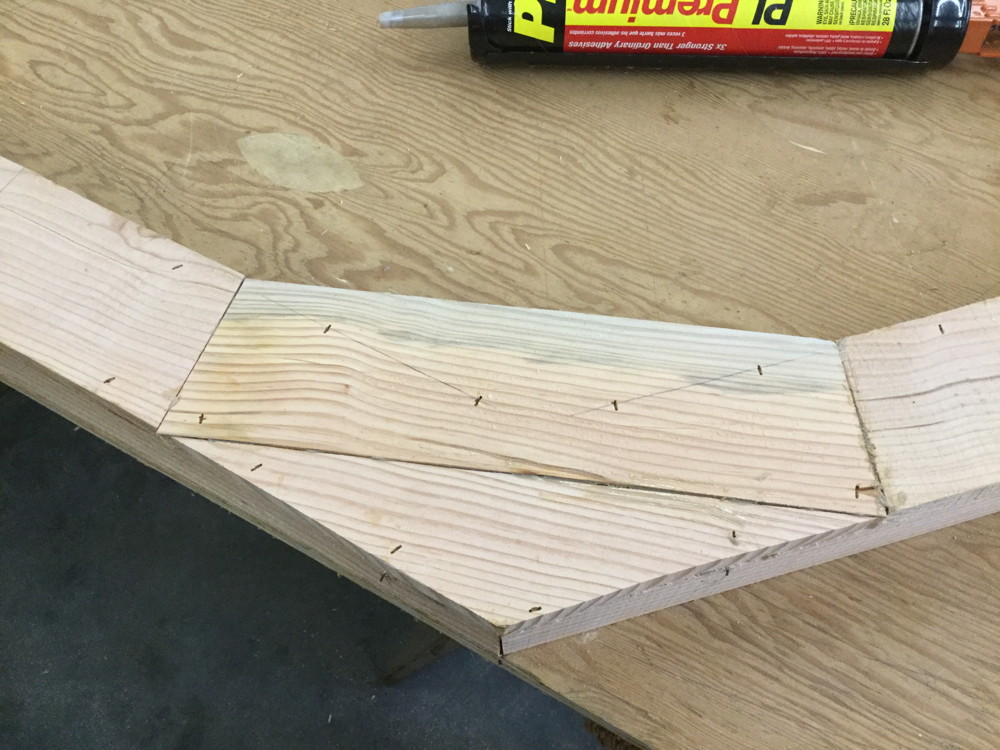
Cut out the 96 face pieces and assembled the face on one side of the first wheel.
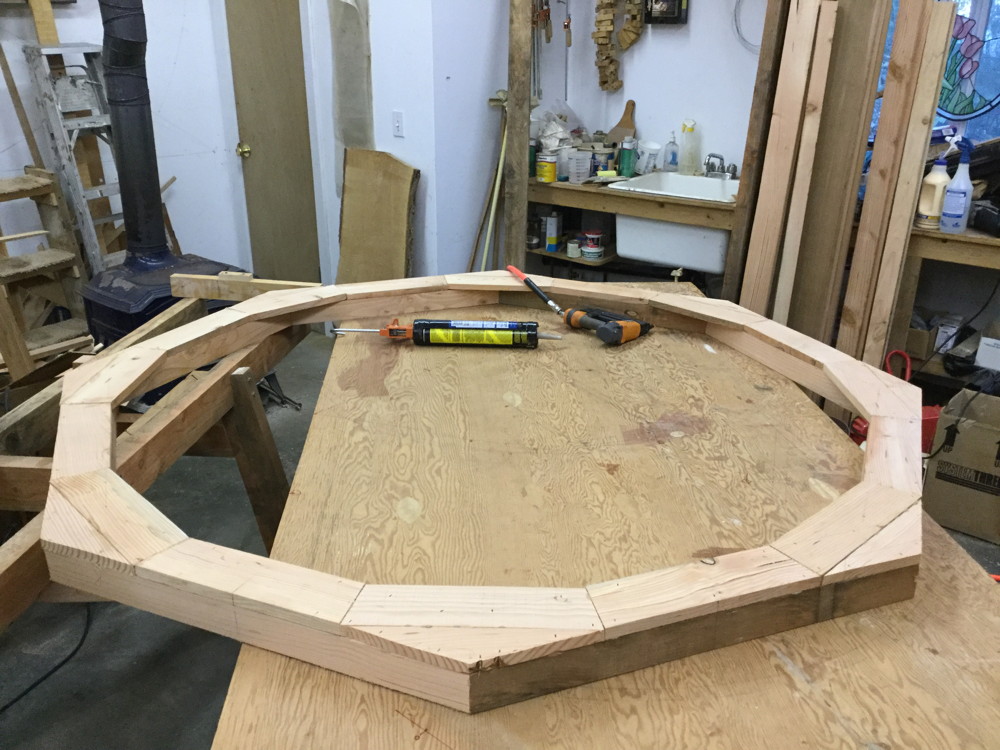
Nov 27th - Attached back face to first wheel and trimmed with router. Fabricated HDPE feet for the wheels and attached to the first wheel. Attached first face to second wheel.
Nov 28th - Bought more adhesive and bolts to attach wheels to mold box. Finished second wheel except trimming last side and attaching feet.
Nov 29th - Finished trimming and adding HDPE feet to the second wheel. Completed all the plywood cuts for the box. Rearranged the shop to try to gain enough space for the box/wheels but will have to move the kayak to have enough room to walk around it.
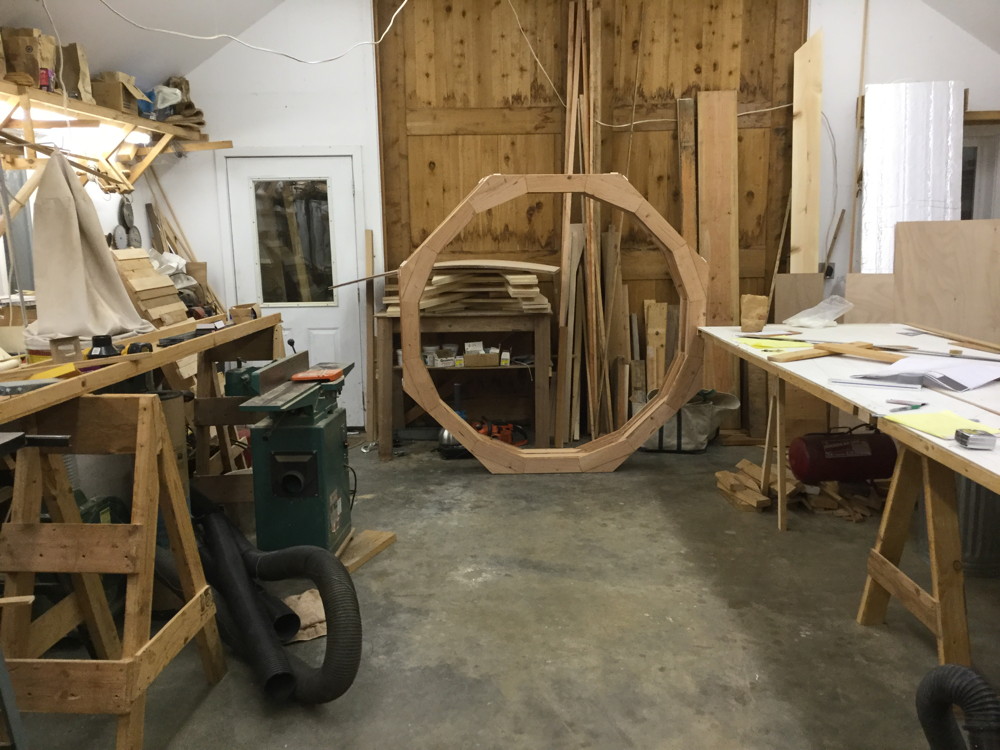
Dec 1st - Assembled ends and side of mold box and bolted one end to one of the wheels with the sides held with screws. All is looking just as I had hoped so far.
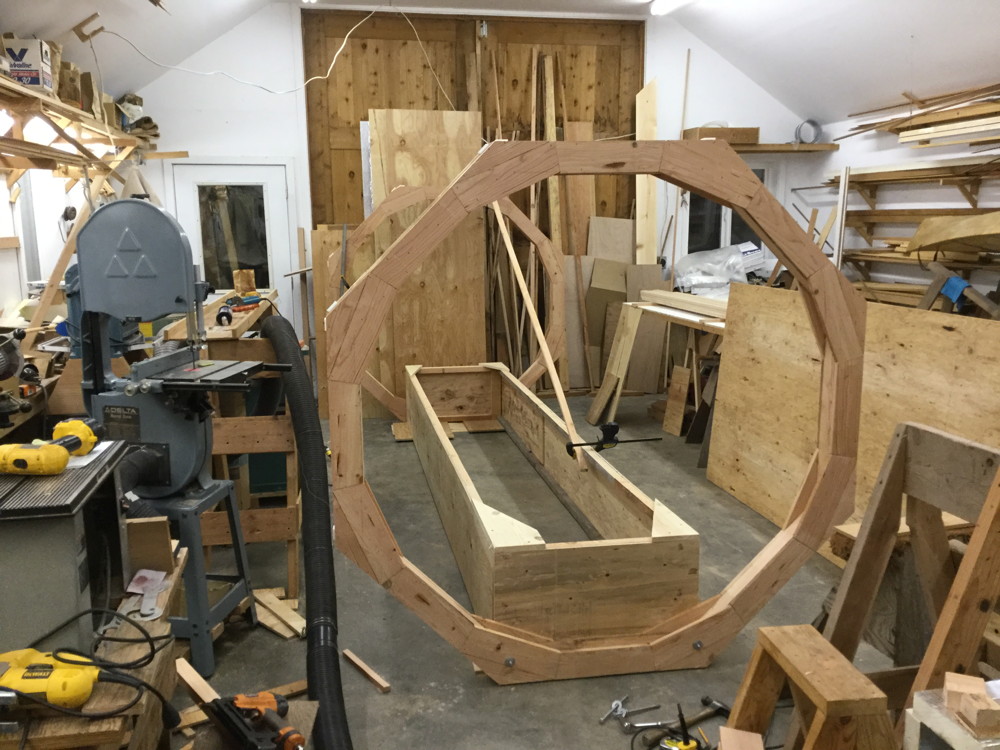
Dec 2nd - I made a trip to the lumber yard for more glue and also bought 5,000 3/4" staples. (the 7/8" staples come through when stapling 1/2" to 1/2" but these don't. Also these are bare galvanized and they hold better I discovered.) Attached ends to sides of mold box and bolted the remaining end. I goofed yesterday and forgot to allow space for the bottom so I had to redo the bolts on that end. The wheels came out perfectly plumb and the box corners square. I laminated the stem after dinner. Since my epoxy metering pumps aren't working, I had to mix the epoxy in 4 separate batches because the balance beam can only manage 6 oz cups. (It takes two 6 oz cups to make one 4 oz batch because I pour back and forth while mixing to insure I get a good mix.) That kept me in the shop until way past my normal bed time.
Dec 4th - I tried to roll the box upside down to add stiffeners and put on the bottom panel. With only the top screwed on the box twists way too much. So, I had to resort to using 2x4 levers to get it to 135 degrees in 1/16th turn increments. The box is positioned to balance with the wheels only when the molds and ribbands or planking are in place. I installed the bottom panel, rotated it back to box at bottom, and installed the bracing and top panel.
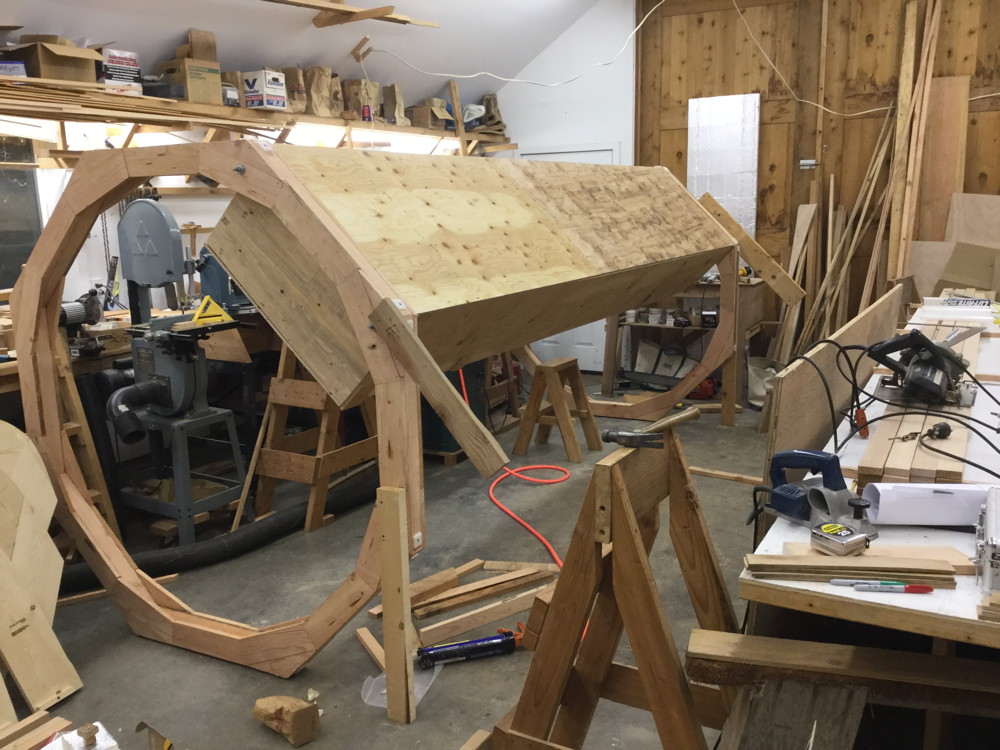
Dec 5th - Installed the molds and sprung a ribband over the center of the molds.
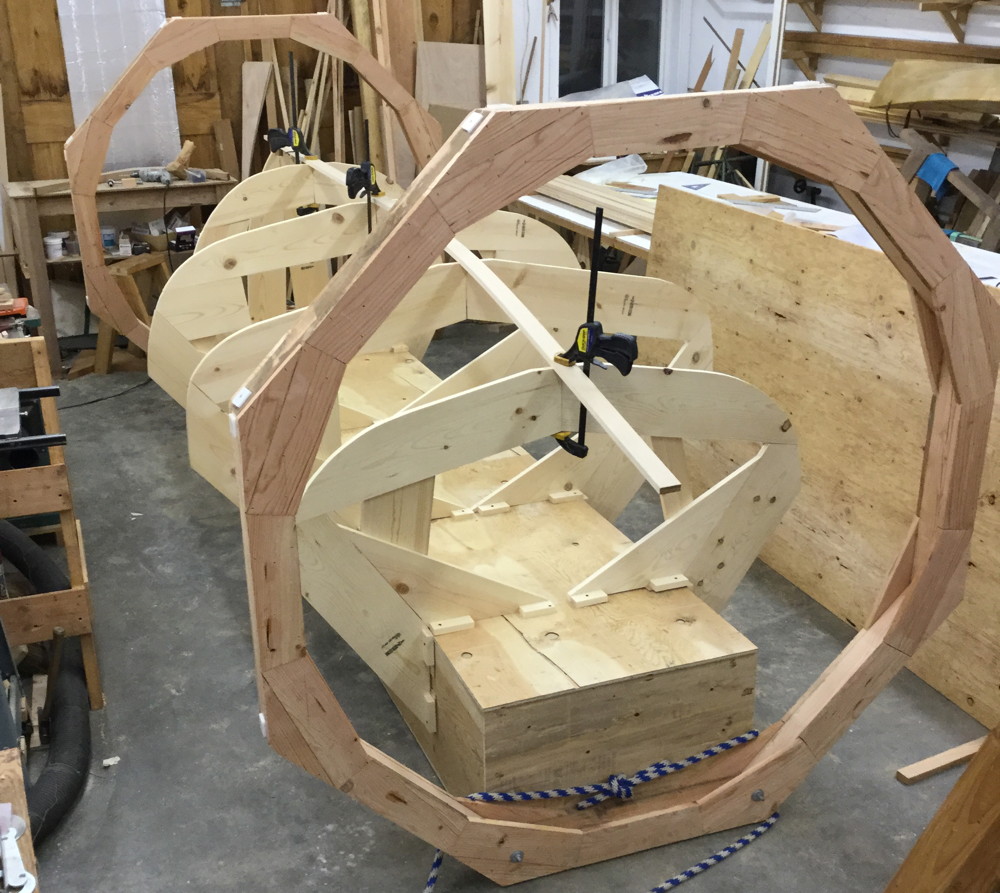
Dec 2015 - I glued the extra pieces I cut for the wheel into a Christmas star and attached to the big shop doors for the holidays.
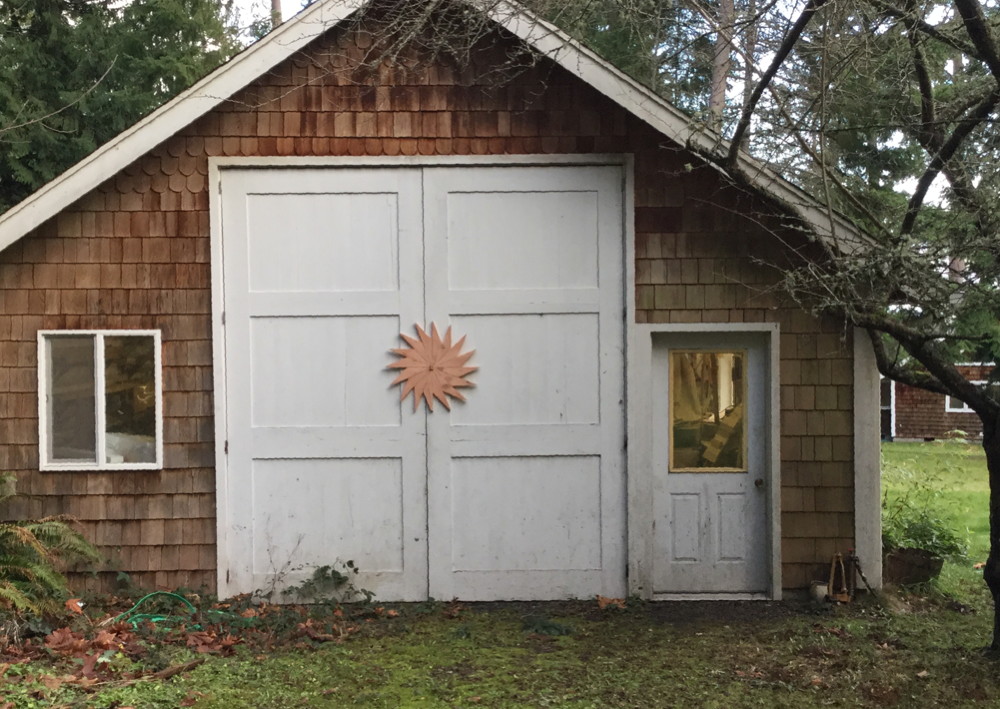
Jan 29th, 2016 - As planking progressed I found that 45 degree turns were too much and the box weight needed to be balanced to keep the wheels more stable. Changed to a 16 point wheel and added a counterweight.
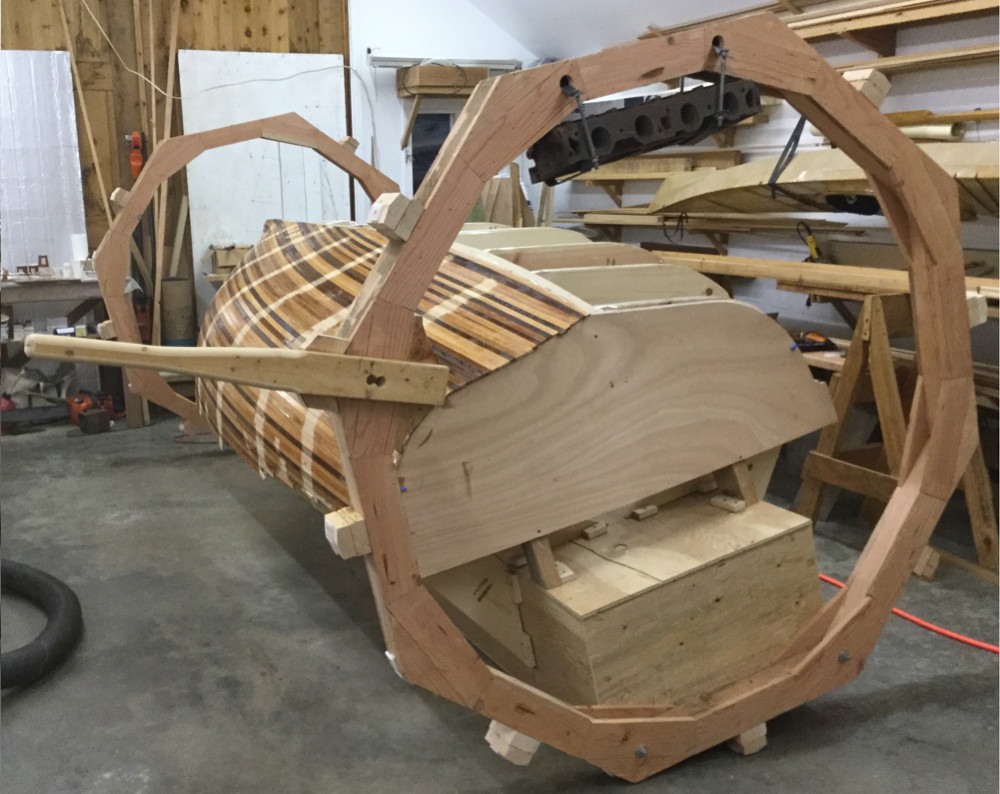
Feb 15th - The added weight of planking was still making rolling difficult so I decided to raise the box on the wheels to bring the mass into better balance. This makes rolling the hull much easier.
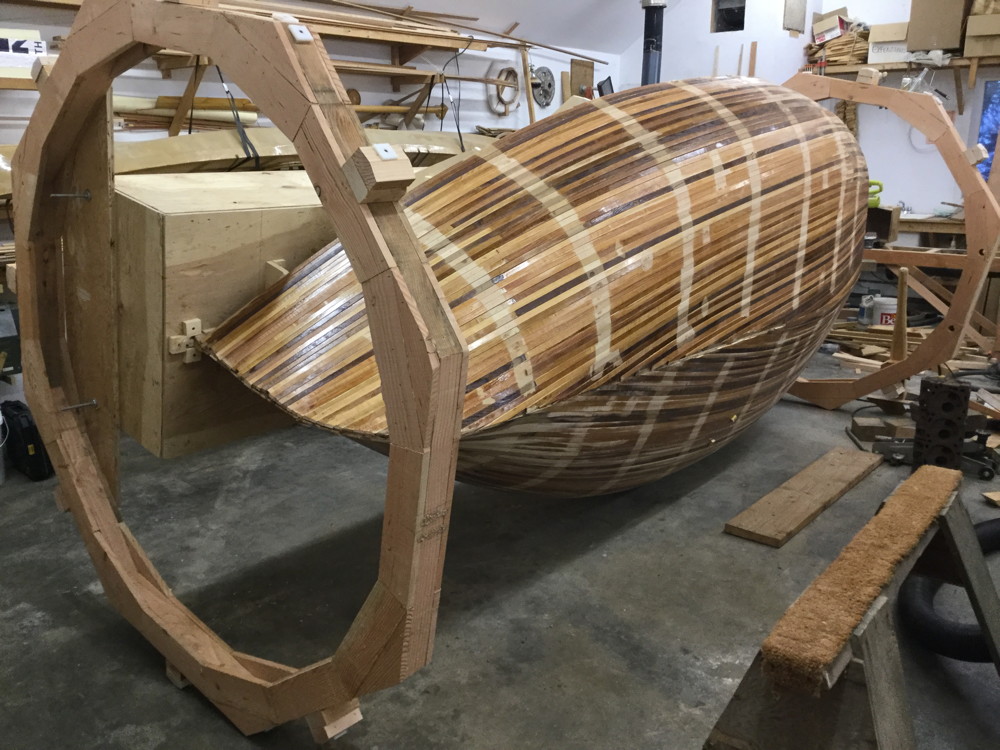